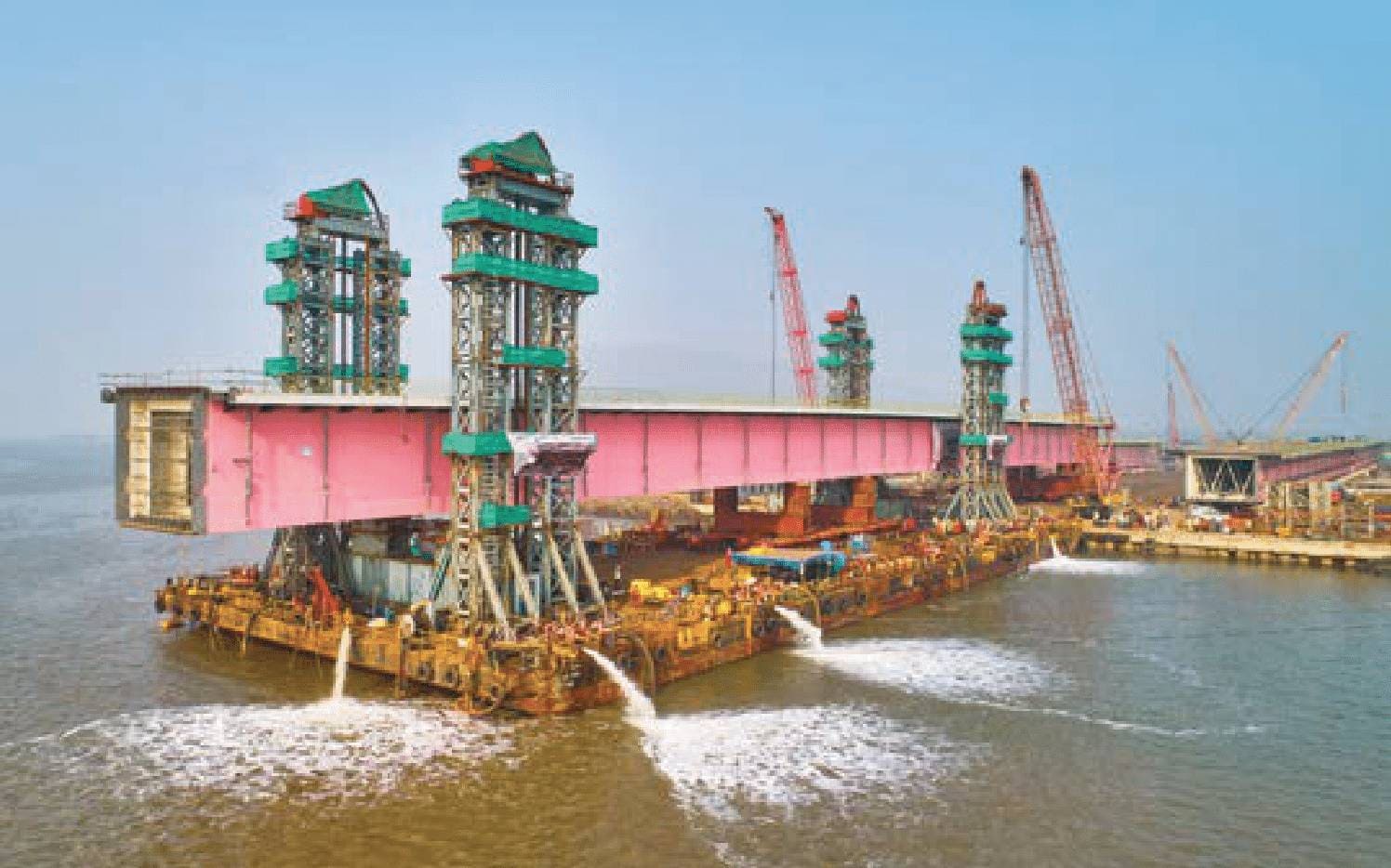
Cited as an engineering marvel, the Mumbai Trans-Harbour Link (MTHL) is one of India’s major infrastructure projects. Set to be launched later in 2023, it is a 22-kilometer, 6-lane sea bridge that will connect South Mumbai to Raigad, a part of the mainland. Being a linear and densely populated city, Mumbai constantly struggles with traffic snarls. The bridge is expected to reduce travel time between Navi Mumbai and South Mumbai from the current two hours to 20 minutes. This will come as a major relief for a large section of the city’s population.
Earlier this year, the J M Baxi Heavy team ferried via sea, varied-sized bridge spans for the project, including the heaviest and longest - weighing 2200 ton, spanning 180 meters, and a width of 14 meters. This portion of the bridge is the equivalent of around 15 blue whales and is close to the world’s tallest statue in height.
J M Baxi Heavy was involved in the transport of various parts for the bridge project which were divided into 3 sections for fabrication. These were awarded in parts to separate companies – two to L&T IHI and one to Tata Daewoo.
With the L&T consortium, J M Baxi Heavy was involved in the handling of the vessel that arrived with smaller sections to the port, transporting them to the yard to assemble the sections into larger units. For Tata Daewoo, while the ask was the same, the J M Baxi Heavy team had to additionally ferry the cargo on barges including towing the barge from the Karanja jetty to the erection point. The barge was strengthened to bear a concentrated load, since the lift was to be done using four points.
The construction of this bridge is a marvel and has never been done in India. The bridge sections were fabricated in smaller sections across different countries - Japan, China, Indonesia and later shipped to Mumbai. The sections were then discharged, stored and transported to the fabrication yard located in Mumbai (for L&T) and Karanja (for Tata). Once the bridge sections were transported to the fabrication yard, they were assembled based on the span required and designed for installation work. The assembled sections varied from 40 meters to as long as 180 meters with weights ranging from 900 ton to 2200 ton. The assembled Orthotropic Steel Deck (OSD) was then loaded on the barge by using a skidding system/ trailer load out, as per the client’s specification. Once loaded on the barge the barge was towed by tugs to the installation location. The barge was then slid into the gap between the 2 piers and then lowered onto the pier caps. This was the most critical part of the installation.
The barge, Aqua Float 330 was utilised for all heavy loadouts and for placement on the pier.
Fun facts about MTHL
It will be India’s longest and the world’s 10th-longest sea bridge to date.
Around 1,70,000 ton of steel bars, equivalent to the weight of 17 Eiffel Towers, have been used.
9,75,000 cubic meters of concrete, was used to construct the structure, which is six times the concrete used for the Statue of Liberty.
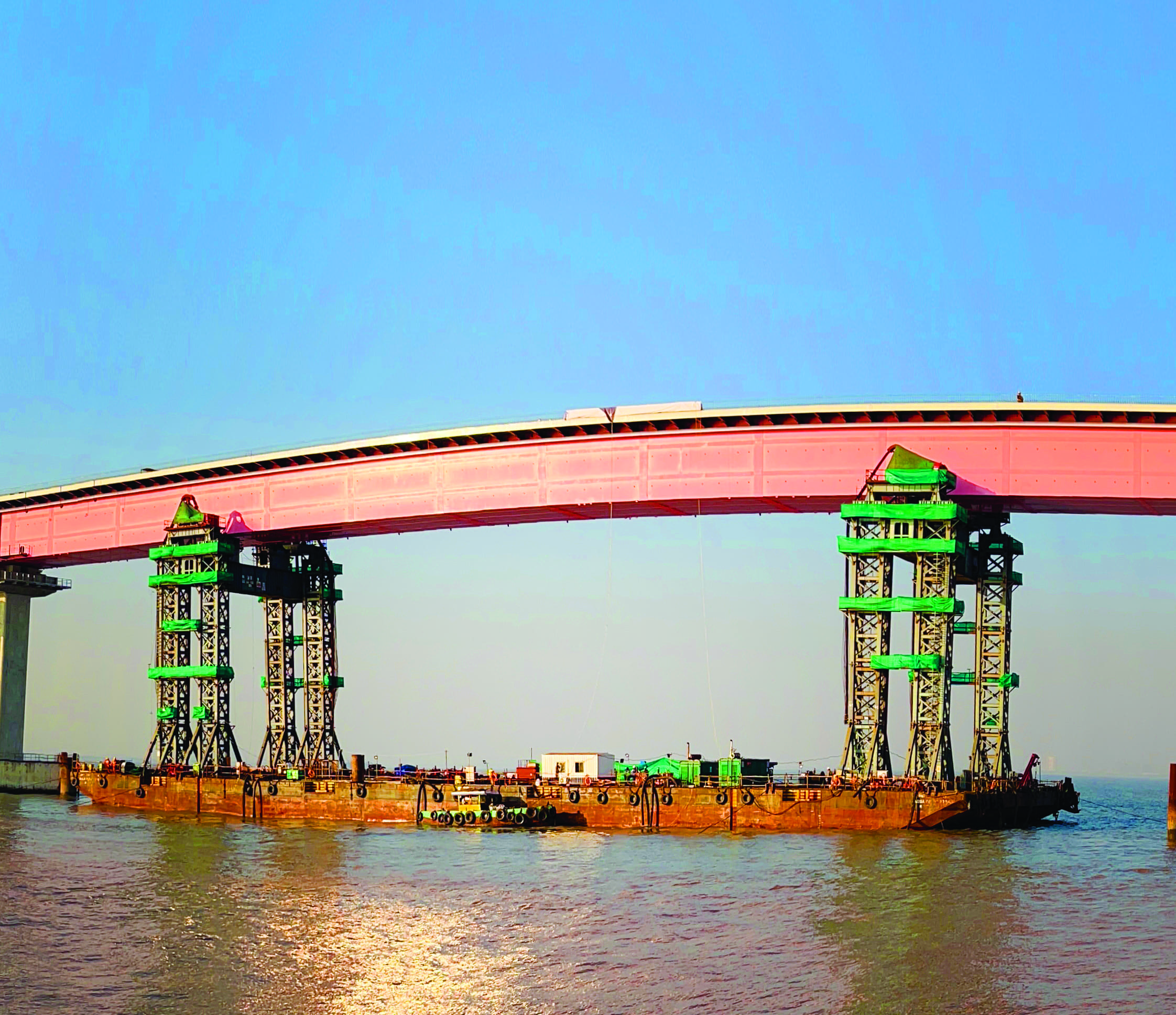