The global health crisis caused by the outbreak of Covid-19 has landed shipping trade into disarray. Ships carrying oil and cargo are stranded at sea for months due to lack of clarity from ports on vessel quarantine, crew change policy and Health and Safety Executive (HSE) checks at ports which, in turn, has pushed the international supply chain towards economic slowdown. This situation eventually left Indian ports in chaos as COVID-19 lockdown hit operations, affecting the ability of traders to move the cargo in and out of the country.
J M BAXI GROUP which operates 5 container and bulk terminals at various ports, namely, Visakhapatnam, Haldia, and Paradip are on the East coast of India and Kandla and Rozi on the West coast. In addition, it operates Container Freight Station (CFS’) at Mumbai and Visakhapatnam and at Inland Container Depot (ICD) Sonepat near Delhi. Three of the facilities at Mumbai, Sonepat and Haldia because of high incidence of COVID-19 patients were declared as Red Zone, thus making operations difficult to continue despite of the logistics being categorized as an ESSENTIAL SERVICES. Volumes took a plunge, given the first-mile (cargo evacuation from port) and the lastmile (supply-chain between ICDs to company warehouses) being severely restricted which posed immense challenges.
- Waiver of Demurrage Charges at Ports
Immediate impact of COVID-19 lockdown lead to a slump in trade demand and traders were left with no option but to shut industrial production. Acute shortage of drivers to move cargo and labour to de-stuff the cargo also leads to a closure of a number of warehouses. This also resulted in the importers unable to custom clear their landed laden consignments and on the other hand export consignments were also held up as a number of vessels skipped vessel calls for fear of subsequent penalties. However, the Government of India which was in constant touch with the maritime community took actions vide and issued an advisory for non-charging of detention charges, ground rent or any similar penal charges from 22nd March 2020 to 14th April 2020 for containerized cargo and extension upto 3rd May 2020 ( i.e the period of lockdown) for non-containerized cargo. This, however, lead to another challenge as container and cargo piled up at the terminals leading to congestion in a matter of just 3 to 7 days from the lockdown issue order.
- Shortage of Truck Drivers and Labours at the terminals
The container and truck moving IN and OUT of the terminal fell by 50% due to reduced number of trailers and unavailability of drivers. Though the government allowed movement of cargo trailers under essential goods and services, the ground reality was far from satisfactory. The truckers were stopped at every check-point just a few kilometers apart making cross-border and provincial border travel challenging. And with the lockdown shutting down highway food establishments and workshops, truckers couldn’t get the services they needed even if they were on the road. ICD and CFS operations on the other hand, were adversely affected due to the slowdown/shutdown of factories owing to non-availability of labour.
Fear psychosis due to COVID-19 virus, absence of work, entry restriction from local villagers, and lack of sustenance in the cities and transportation hubs had created panic amongst most drivers and labour who then started moving back to their native places.
- Lack of Storage Yard Capacity at the Terminals
Congestion at the terminals increased as import containers moved to the nearby CFS’s were not being cleared by the importers and custom house agents to combat the spread of COVID-19 during the lockdown period. This resulted in a pile-up of a large number of import laden inventory in the CFSs and ICDs, and with only a fraction of the imports being gated-out by the trade, these terminals were facing an unprecedented challenge as most of them reached their “holding capacity”. Empty depots with no operational staff lead to an increase in empty boxes at the terminals.
- Increased Load on Rail Traffic and Congestion
With a shortage of truck drivers for road delivery, it leads to the movement of hinterland container traffic by rail. This surge in rail traffic chocked up storage capacities at all ICD terminals with limited operational resources, nonavailability of custom authorities and truck drivers for evacuation and local hinterland delivery to consumption centers.
- Challenge on Equipment availability, repair and maintenance
With terminal facilities overloaded with import consignments and clearance issues stressed up available container and cargo handling equipment. It was difficult to add on handling equipment capacity or mobilize from a distance where equipment were available due to provisional border restrictions and drivers’availability. Routine maintenance and an Annual Maintenance Contract (AMC) support was critical to keep equipment running but with the lockdown the availability of consumables locally and maintenance support from vendors was next to impossible due to quarantine measures and closed establishments.
- Challenge on safety measures and supplies
The imposition of a sudden lockdown and a quarantine advisory increased demand for sanitizers, thermal screening instruments and personal protective kits. With most of the required essentials being out-ofstock for weeks, operational safety was a major concern at ICT terminals leading to hinderance in vessel operations and gate movements. Outside staff, drivers and labours were reluctant to perform normal work under such a severe situation.
- Operating in Extreme Conditions
Natural conditions added nonadvantage during this crisis as temperature rose every day after relaxation; tremors of earthquake, rain and storm affected working scenarios also.
Despite challenges the staff at ICT terminals complied with all regulatory precautions and safety measures to ensure the port and inland terminals at respective locations remain fully operational with minimum on-site working staff and rest to operate from home.
- Sorting Storage Concerns
In limited time all ICT Terminals with pro-active moves and innovation ramped-up cargo storage capacities. ICT CFS at Mumbai was the first to obtain permission from Customs to allow storage of import containers in non-custom bonded facilities used for container operations. Additional space arrangements at nearby CFS for overflow containers was also resorted to. ICD Sonepat and ICT Paradip terminals ramped up facilities including development and having it custom notified within 15 days under adverse quarantine conditions with limited resources but with complete safety measures to create additional storage capacities. The empty containers at CFS and ICD were relocated to nearby yards for ease of operations. These measures enabled ICT terminals to respond to congestion issues right in time.
- Boost Cargo Evacuation and Last Mile Deliveries
ICT teams also embarked on moving food grains and other essentials for million of Indians that rely on services which connect these terminals to remote hinterland. ICT terminals through the network of port authorities, suppliers, drivers and manufacturers, even struck key player partnerships to pool resources to ensure that movement could continue, from cross-border to intra-state and last-mile deliveries. Terminals coordination with railway authority came very handy as the tracks were totally free of passenger traffic and the railways were able to move the cargo from gateway ports to the hinterland, taking away some of the load from the ports. For container traffic, railways announced free of cost empty container and flat movement during the second and third phase of lockdown which helped operators to move rakes swiftly on the railways network which ensured customers timely cargo movements to and from ports.
- Safety Measures to Build Confidence in Drivers, Security and Staff Members
Operations Team at ICT CFSs and ICD went all out to hold and bring back available drivers assuring them of their health and safety, while evacuating containers from the terminals so as to minimise the impact as 50% of them left for their homes before the lockdown. Drivers were incentivized on per trip basis to increase participation. Terminals made sure sufficient sanitization and personal protective kits were made available despite scarcity in the local market to terminal staff, vessel crew, drivers and labours to perform normal operations. Conducted an awareness session on the lockdown guideline and social distancing at all terminals. Offered food and essential supplies to drivers and labours at the terminal to assure them protection without quitting their work.
ICT on-site employees were provided with the required Personal Protective Equipment, Sanitizers etc. Terminal premises and the offices were quarantined on a periodic basis. Personnel arriving in the terminal are thermally screened at the entry as a precautionary measure. Terminals marked all the interaction places, like service centre, warehousing, customs area, customer service, rail yard, CFS and cargo examination area.
- Mobilize and Add Equipment Handling Capacity during critical times
In the month of April - May 2020, Paradip Terminal saw a spike in steel volumes. With scarcity of handling equipment locally, cranes were sourced and mobilized from West Bengal and Visakhapatnam to Paradip despite quarantine restriction on road movements and managed to maintain the cargo handling rate at the terminal. Additional reach stackers were quickly mobilized from nearby locations which were underutilized to maximize yard handling capabilities for faster turnaround and ease congestion. The teams showed exceptional skills to manage spares and consumable supplies to equipment, undertake maintenance works without AMC support and ensured no equipment breakdown during such critical times.
- Promoted Digital Mode to speed up transactions
ICT terminals urged all stakeholders including importers, carriers, truckers and custom agents to adopt digital mode for online payment transfers, invoices, delivery orders and out of charge receipts for final container delivery. To support the trade all documentation / delivery / payment counters at ICT CFSs and ICD were kept open for normal working hours to maintain streamline communication at all times.
Delhi International Cargo Terminal
DICT known as ICD Sonepat which is strategically connected to the country’s northern hinterland was severely affected by the lockdown but continued to operate despite limited manpower, over capacity, liaisoned with local authority to ensure all permissions were in place to enable normal operations and now are handling an average of 3 rakes on a daily basis.
Visakha Container Terminal
VCT handled the highest rail bound container movements during the lockdown month of April 2020. 60 rakes were handled during the month carrying 8,446 TEUs which is the highest number of rakes and rail bound container volumes handled in a month till date.
Paradip International Cargo Terminal
PICT a multipurpose terminal could manage to handled 2.25 lakh metric tonne with 86 steel rakes amidst lockdown and endless restrictions.
Haldia International Container Terminal
HICT container terminal was in a red zone and despite the lockdown it ensured pick and drop facility and deployment of skeletal staff to have continuity in operations. The terminal resumes operations in 32 hours after Cyclone Amphan crossed West Bengal.
HICT Engg team developed in-house Contact Free Hand-wash System at Haldia Dock Complex. Inaugurated by Shri. A. K. Dutta (GM - M&S) and Mr. A. K. Mahapatra (GM - Traffic) and other senior representatives from Haldia Dock Complex and HICT
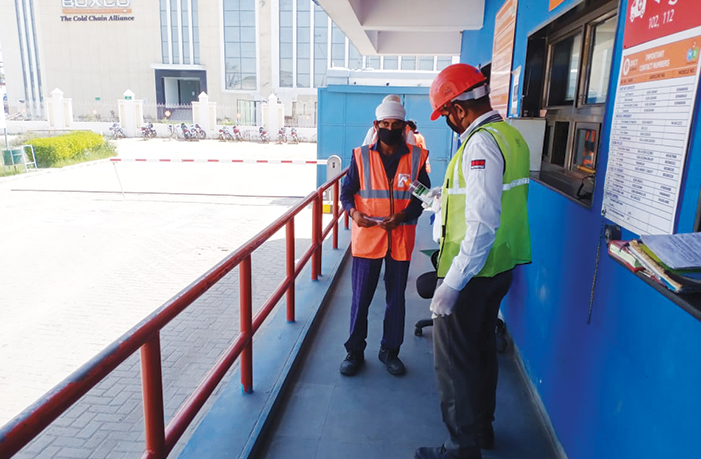
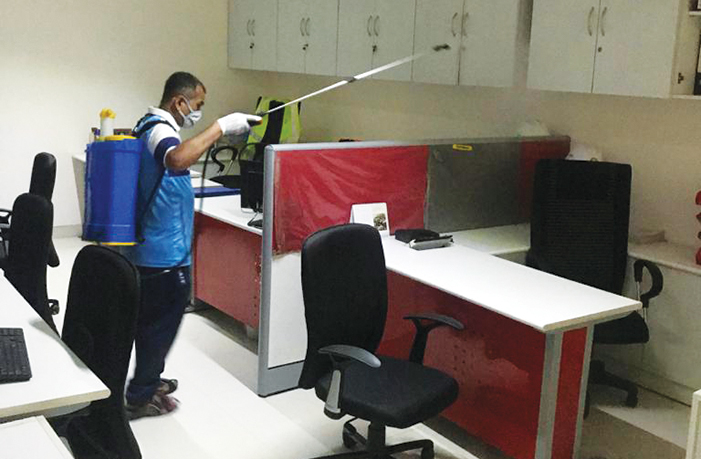
MICT CFS is committed for safety and health of working staff and our values customers. Carried out the complete facility disinfection.
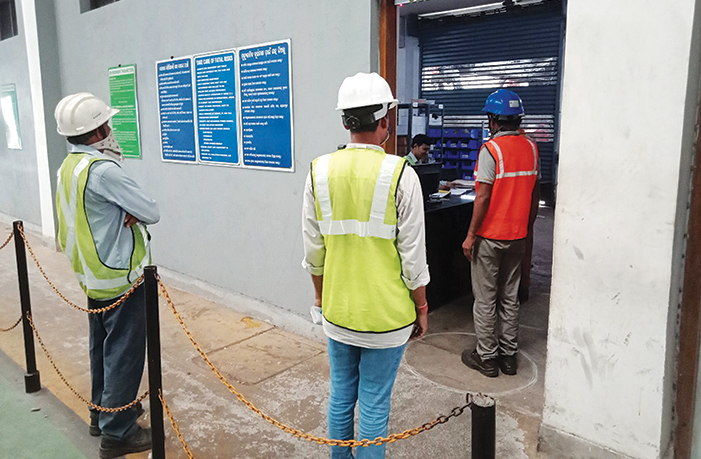
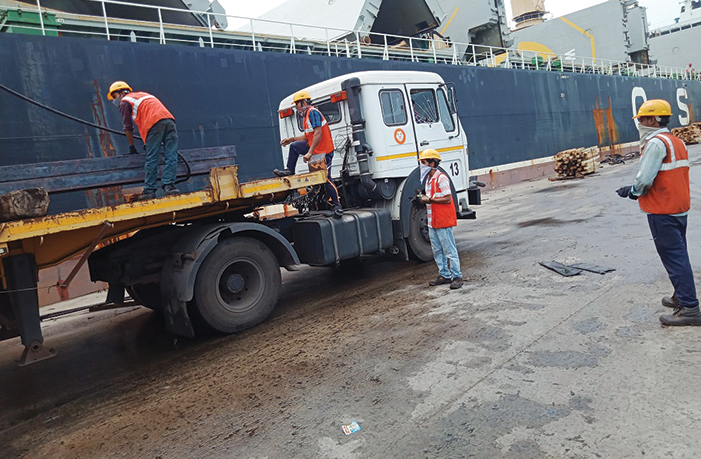
A relative approach by Quality, Health, Safety and Environment Management (QHSE) to combact COVID-19 and appropriately served Hot Milk + Bournvita health drink with banana fruit to every individual associated with KICT.
Social distancing while break-bulk cargo operations, at toolbox meeting and at work followed by PICT terminal staff.
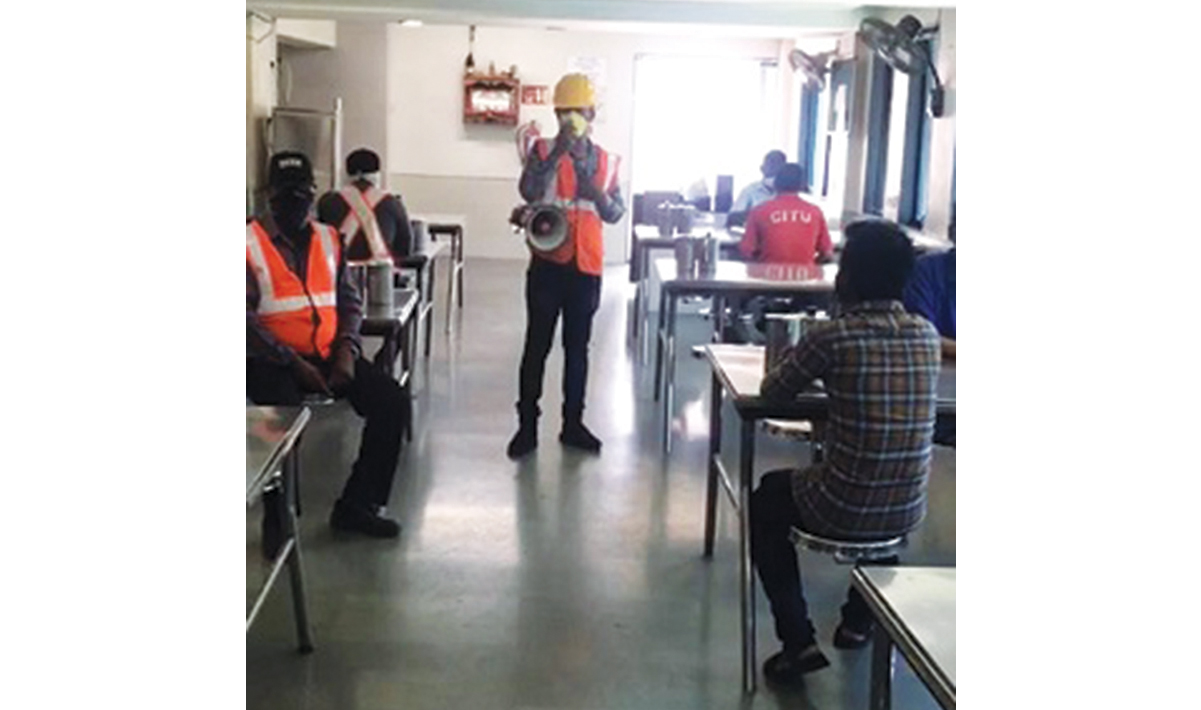
Use of mobile public announcement system by MICT CFS each hour from 10:00 hrs to 20:00 hrs to spread awareness and precautions to be taken.
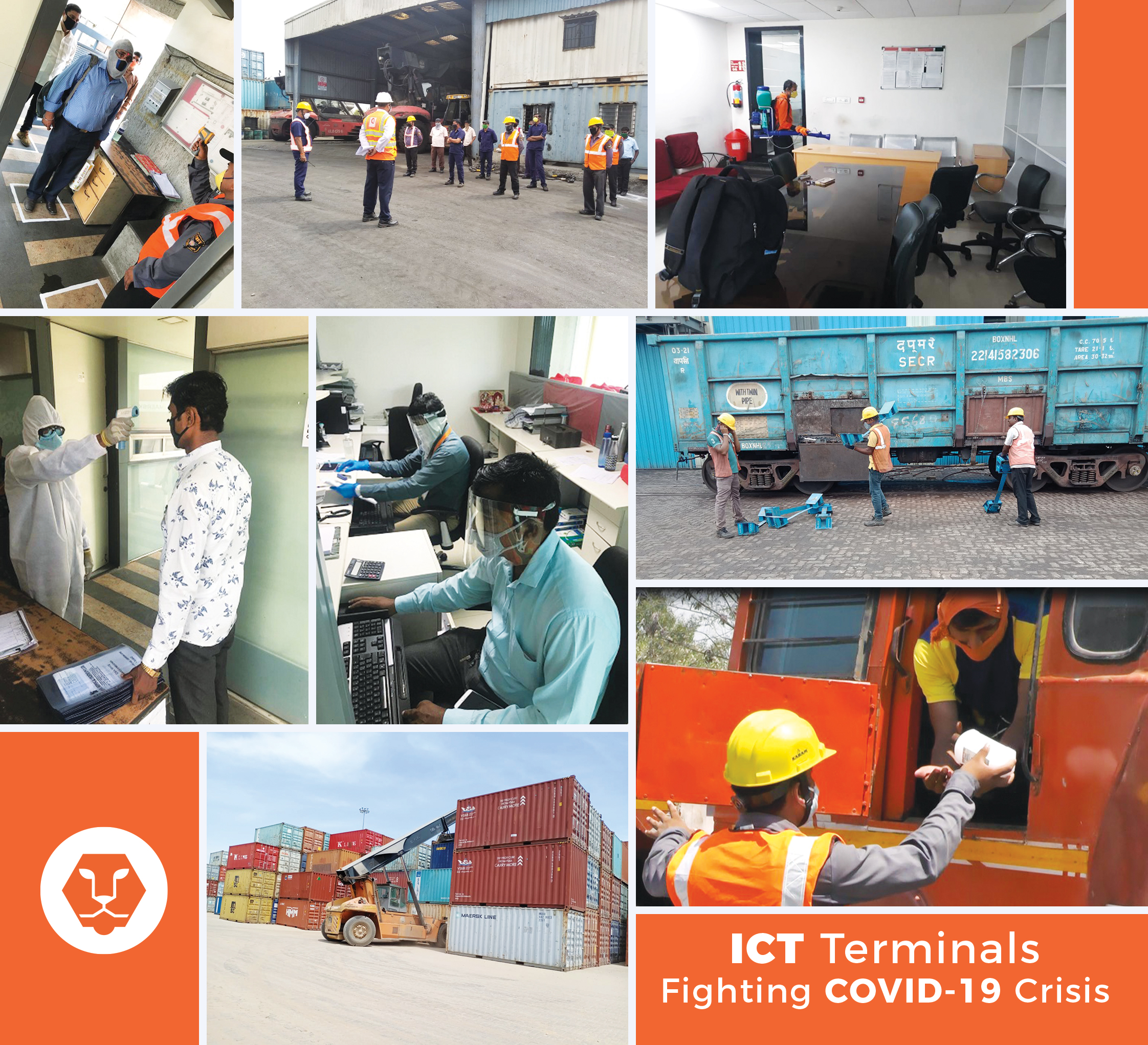
- Sector Recovery
Ports that have a significant exposure to the affected cargo categories could see a near-term impact on their cargo volumes. From the lows of April, there has been mild recovery in the month of May with lockdown relaxation. While cross border restriction for road movement remains affected, the move towards the coastal movement will pick up taking momentum. As a step towards a self-reliant economy, domestic sourcing and consumption will increase for industries and end users, which will further strengthen the supply chains.
Furthermore, the immediate term growth prospects of the sector also remain subdued and the domestic logistics sector is expected to contract in the current fiscal. The extent of the impact will depend on the duration of the slowdown in consumer demand and industrial activities due to COVID-19 and the pace of the subsequent recovery.
An innovative approach, optimizing operations digitally, and relying on flexible and scalable business continuity and contingency plans seems to be the best way ahead for stakeholders in shipping and logistics.
Amidst all these challenges, compared to other ports on the West and East Coast of India, it is prudent to say that ICT Terminals are COVID-19 proof with records growing even during these testing times.