Steel is the most commonly used material in the world. Every year more than 2 Bn ton of steel is manufactured, which makes it responsible for approximately 8 percent of the total CO2 emissions globally. This makes the steel industry one of the most polluting and energy-hungry industries on the planet. To fight the environmental impact the industry causes, de-carbonizing steel has become the need of the hour. Major players like Tata Steel, JSW are already making efforts towards making steel sustainable. While recycling steel and its products account for 26 percent of global demand, manufacturing of steel through sustainable sources is key. Green steel is manufactured without the use of fossil fuels. It uses low-carbon energy sources such as hydrogen, coal gasification or electricity instead of the traditional carbon-intensive manufacturing route, through coal-fired plants. The use of green steel will eventually lower emissions, cut costs and improve the quality of steel while also reducing the industry’s carbon footprint.
To produce green steel, the energy capacity and green hydrogen required would be as follows
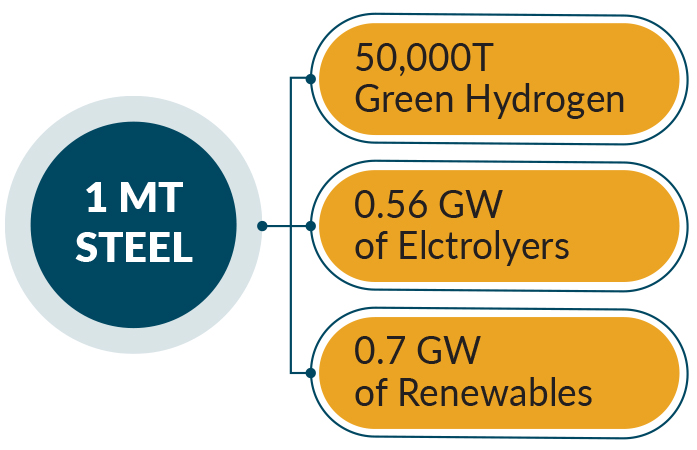
The green steel method uses hydrogen to reduce the iron pellets in sponge iron/metallic iron that can be used to produce steel. This process is done below the melting point of iron (800- 1200C) saving energy costs.
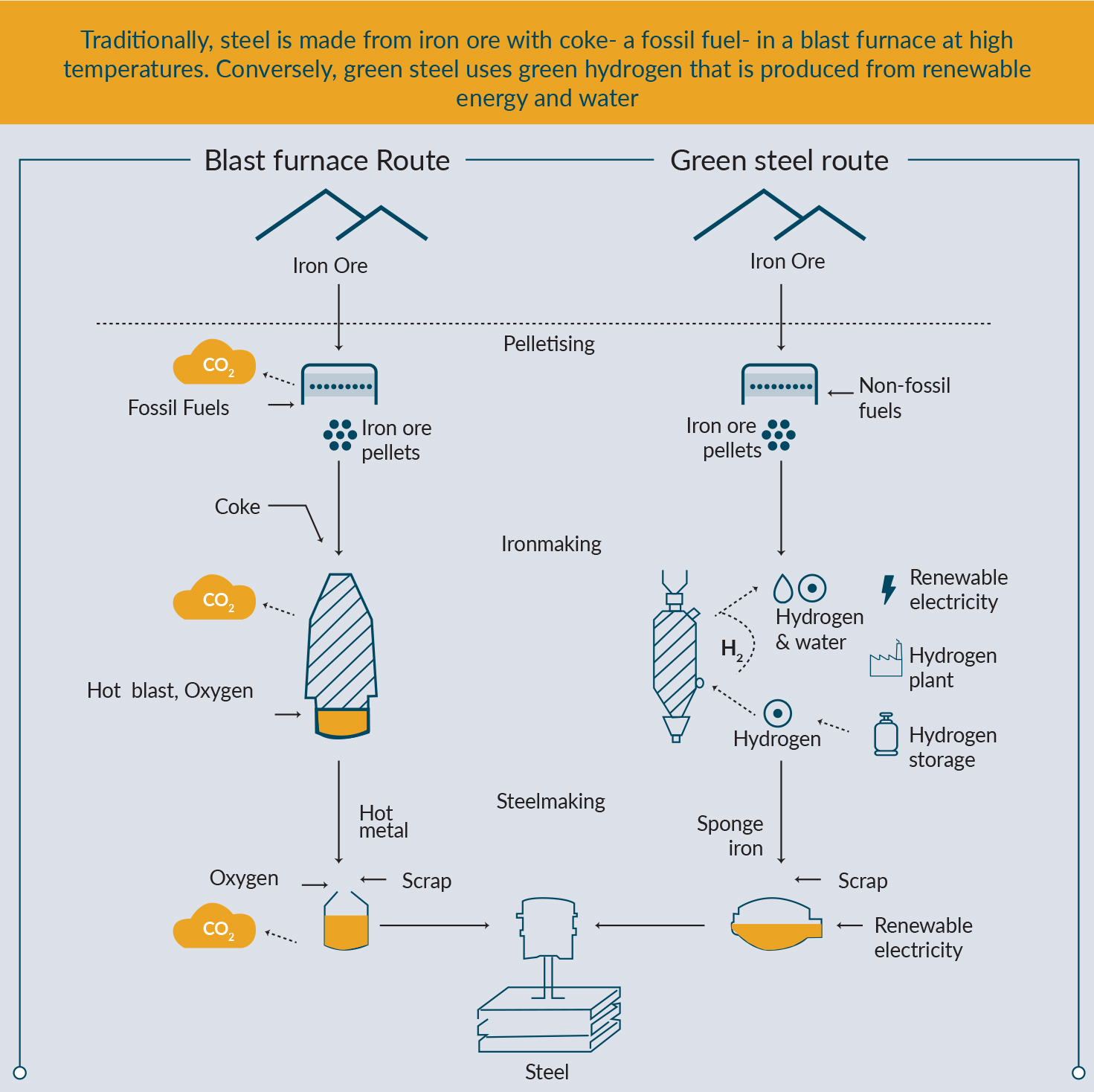
By adopting new processes to produce steel, fossil fuels can be removed from the process and significantly reduce CO2 emissions
Steel production source | Annual production (t) | Green Hydrogen req. (t) | Electrolyser capacity req. (GW) | Renewable capacity req. (GW) |
---|---|---|---|---|
U.S.A. | 85.8 | 4.3 | 48 | 60 |
Europe | 103 | 5.2 | 58 | 72 |
China | 1032.8 | 51.6 | 581 | 726 |
Global | 1951 | 97.6 | 1097 | 1371 |
Green steel through scrap
India-based Kalyani Group has launched India's first green steel brand called Kalyani Ferresta.
It is manufactured using renewable energy resources enabling a zero carbon footprint. Ferresta-branded steel has up to 70 percent scrap that is melted over an electric arc, which is powered by renewable energy sources. Through the new method, the company is able to eliminate a total of 76,484 carbon dioxide (tCO2) emissions, minimize water consumption by 10 percent, and was able to recycle 99.4 percent of its waste
Demand for scrap will rise to 65 Mn ton per year by 2030. To ramp up steel scrap use, the country will have to improve both its collection processes and bring more scrap supply into the organised sector.
Green steel - the need of the hour
According to ArcelorMittal Nippon Steel India, the iron ore and steel industry globally accounts for around 8 percent of total CO2 emissions on an annual basis, whereas in India, it contributes 12 percent to the total CO2 emissions. With such high emissions, steel producers in India and globally are facing escalating pressure from governments and investors, to reduce their carbon footprint from both environmental and economic perspectives. The Indian steel industry needs to reduce its emissions substantially by 2030 and hit net-zero carbon emissions by 2070. This is where green steel comes in.
Decarbonizing the steel sector is also important from the perspective of the emerging international regulatory landscape. For example, the European Union (EU) is set to charge a tariff on carbon emissions from steel imports from 2026 under its Carbon Border Adjustment Mechanism (CBAM), which is expected to be equal to the carbon price paid by European producers in the EU carbon market. As of 2019, the average emissions intensity of Indian steel was approximately 2.06 of carbon dioxide per ton, compared to the global average of approximately 1.45 per ton. This could put Indian steel exports at a disadvantage. Without any additional effort to decarbonize, Indian steel exports to the EU could fall by as much as 58 percent in 2030.
Green steel initiatives
In recent decades, the steel industry has achieved significant reductions in energy input and CO2 emissions intensity. Increasing use of Electric Arc Furnaces (EAFs), as well as utilization of waste heat recovery technologies, have contributed to about 61 percent reduction in energy consumption per ton of steel produced since 1960. However, these improvements have not been sufficient to reduce the total absolute greenhouse gas emissions from steel production. There remains an estimated 15–20 percent improvement potential on the energy efficiency front.
Jindal Steel & Power Ltd. (JSPL) plans to develop its Odisha plant into the largest and greenest facility in the world. The company claims to be the first steelmaker in the world to build coal gasification to produce steel, using clean coal technologies.
Tata Steel's Netherland subsidiary has launched Zeremis Carbon, a green steel solution that offers a 30 percent reduction in CO2 intensity as part of its aim to eliminate CO2 emissions by 2050. The company has committed to switching to green hydrogen-based steelmaking. It is aiming to reduce CO2 emissions by at least 30 percent by 2030 and to emit 75 percent less CO2 by around 2035, with the ultimate goal of eliminating CO2 emissions by 2050.
JSW Steel has earmarked approximately US $ 1.21 Bn to increase the use of renewable energy to replace thermal power and other green initiatives. ArcelorMittal-Nippon Steel India, a joint venture between ArcelorMittal and Nippon Steel, has committed around US $ 33.5 Mn for various environmental initiatives including a zero liquid discharge system at its Hazira steel complex in Gujarat.
Challenges
There are two basic steel production routes: the Blast Furnace (BF) route, where coke is the primary fuel, and the Direct Reduced Iron (DRI) route, where the fuel can be coal or natural gas. India presently produces around 90 percent of crude steel through the BF and coal-based DRI routes. While hydrogen has the potential to fully replace coal or gas in the DRI process, it is seen to have a limited role in being able to substitute coke in the BF route.
Supporting infrastructure
There is an inadequate support network for the storage, production and transportation of hydrogen. This network infrastructure will have to be scaled significantly to ensure that the green hydrogen demand of approximately 8 ton by 2050 from the sector is met. For Carbon Capture Storage there is a lack of data on the availability of potential geological storage sites and their capacities. A comprehensive national study to assess these capacities is needed.
As India embarks on a journey of becoming a developed nation by 2047, its steel industry should exhibit strength and resilience in the face of a dynamic global marketplace. It must de-risk supply-chains, leverage digital solutions and deliver customerfocused products for world markets. The sector must operate from a position of advantage founded on strong cash flows. This will create enough headroom for making bold investments in ambitious projects to deliver sustainable value for all.