Ports are gateways to the economy and therefore are naturally a flurry of varied activities. However, fuel is one of the biggest expenses that keep port terminals running. In a bid to manage and monitor fuel costs, Paradip Multipurpose and Clean Cargo Terminal with the help of J M Baxi’s technology company - Portall, set up a technology system, replete with sensors and integrated software to capture data on fuel disbursement and usage.
Fuel management systems are designed to monitor and control of fuel consumption within the fleet – port equipment and heavy vehicles. They accurately measure and track fuel inventories and how fuel is dispensed. This vital data is stored in the system and can be reviewed through connected web portals and mobile apps.
The components of fuel management systems are – the tank, the pump, the tank gauge, the fuel management application system and the fuel access device and hardware. All of these components are integrated via sensors and a gateway and software platform.
The sensors are fitted to fuel tanks to monitor fuel levels. The sensors continuously capture and transmit this data real time to a centralized platform.
Whenever the fuel level goes low or there’s a sudden fluctuation in the fuel level, an alarm is initiated from the platform to the user notifying them to refuel or warn of any suspected leakage or pilferage/theft. Additionally, users can also generate daily, weekly and monthly reports to verify and compare the refuelled volumes with the reported fuel entry log to stop malpractices.
A cause for change
Apart from manual process which can lead to grave inaccuracies, there were several reasons which egged the team on to adopt this change:
- J M BAXI's Paradip terminal is a multipurpose clean cargo one. This means that a variety of over 90 equipment types being handled simply because the terminal caters to different types of cargo.
- 60 percent of the equipment is owned and the rest is hired
- Fuel and equipment are major components of operational expenditure
- On average over 120 kilolitres of fuel is being consumed per month to meet the operational requirements
- Receiving and distribution of fuel is a completely manual process
- Equipment engagement and monitoring are carried out manually by the operations team
- Kilometre Reading (KMR) and Hour meter Reading (HMR) is captured manually through a log sheet
- Fuel consumption and tracking is done manually by the operations and engineering teams
- Idle time of equipment is captured and calculated manually
The impact
All the manual processes related to fuel management are now automated – fuel receipt, distribution and consumption, utilization per equipment, equipment maintenance and idle time. All these data points now rest in the fuel management system and can be extracted and customized for generating reports to be studied.
To ensure seamless operational management, the working area is geofenced enabling live tracking of the equipment. Fuel utilization can be controlled with real-time monitoring of fuel in the equipment’s tank. Other Artificial intelligence (AI) features help users to effectively plan the ability of the equipment to handle more volume with less engagement.
It is expected that this exercise which began in May 2023 will reduce fuel consumption by 5-10 percent, and will eventually help reduce the carbon footprint.
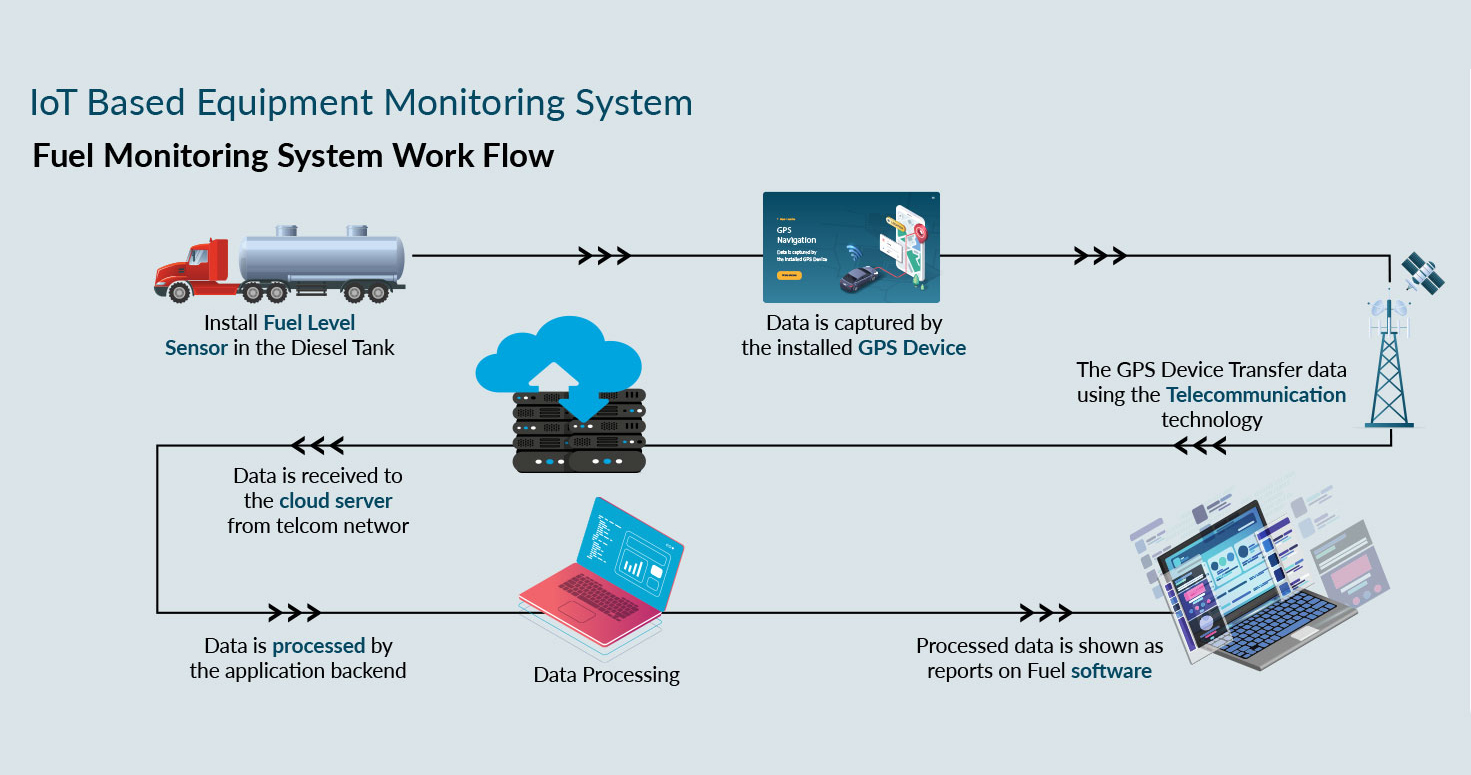