Kathmandu Apparel is a premier exporter of textiles. It is headquartered in Mumbai and has manufacturing units in Bangladesh, China and Vietnam. It was setting up a new dyeing unit in Kolhapur, Maharashtra, and needed an Effluent Treatment Plant (ETP) to remove contaminants produced during the dyeing process.
Wastewater purification is a challenge in the textile industry. A study in Nature found that the industry is highly polluting, more so than airlines and maritime shipping worldwide. It estimated that consumers are buying 60% more clothing than they did in 2000. The textile industry has had to keep pace with increased production. The wastewater generated by dyeing includes fats, oils, chemicals and colours. Treatment facilities are large and complicated due to the volume of water that is used in the production process and the number of steps needed to clean the water.
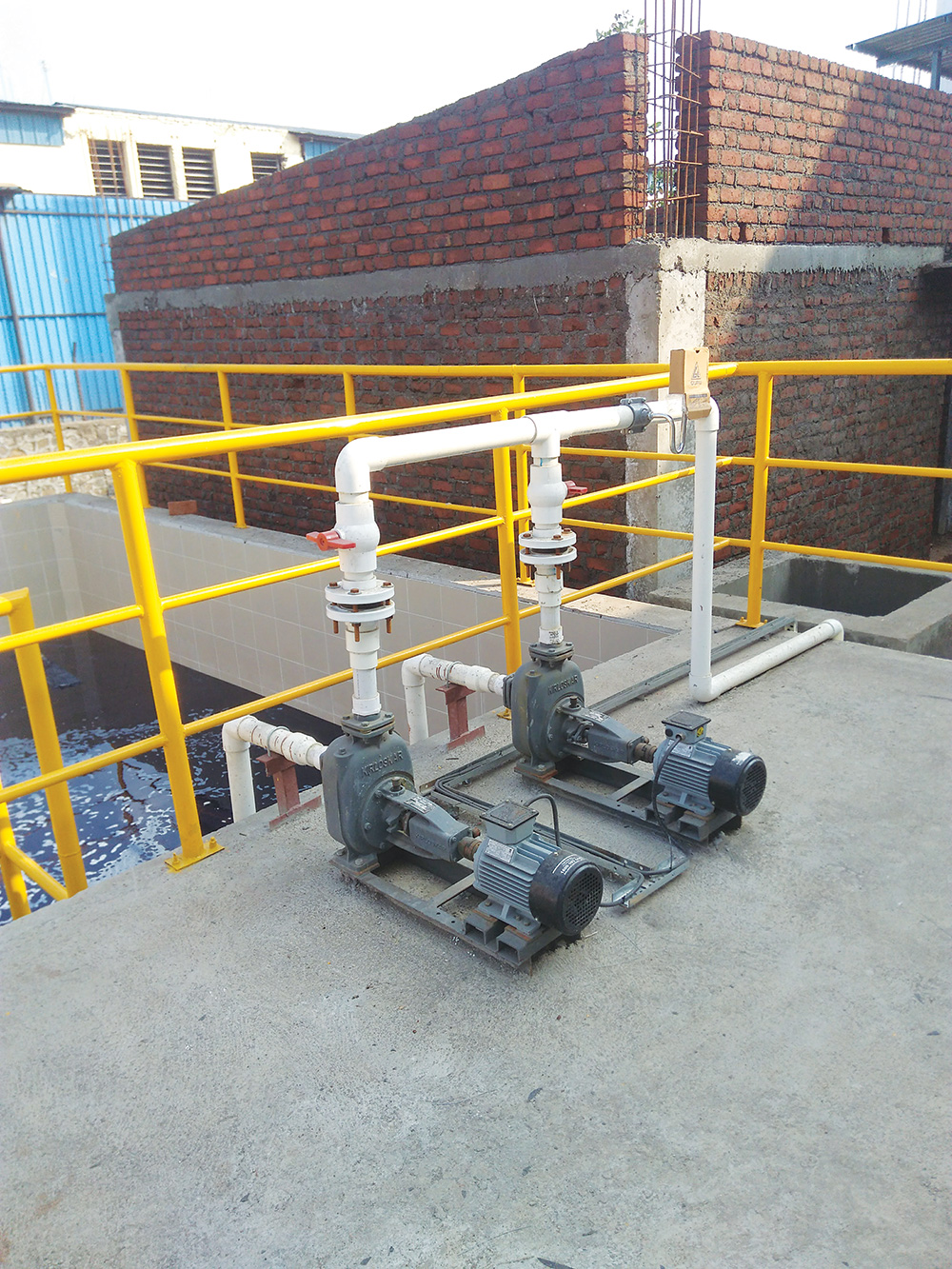
Kathmandu Apparel visited installations in Pali, Rajasthan, and Tiruppur, Tamil Nadu, to study the latest technologies used in textile effluent treatment and shortlisted two companies with whom to move forward. Arya Water Technologies (AWT) was not the preferred bidder because we lacked sufficient experience in the textile industry. However, we were invited to submit a bid, as we had previously delivered a smaller ETP that was running successfully at Kathmandu Apparel’s Mumbai unit.
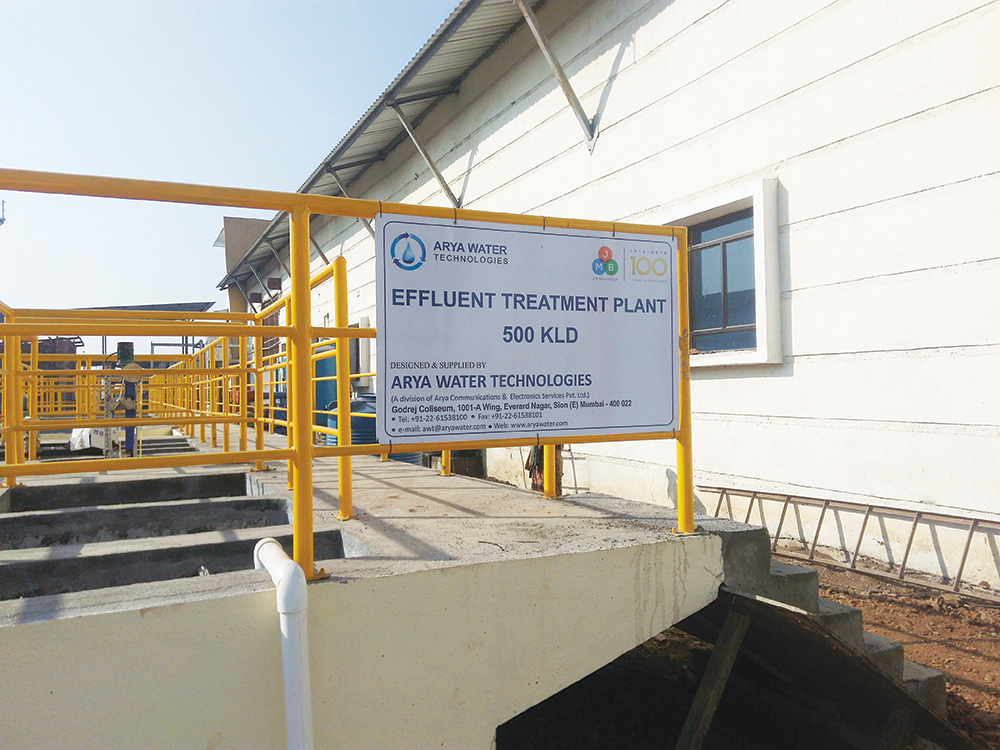
The solution AWT designed incorporated a continuous flow of effluent through the plant. This allowed for pretreatment with chemicals to remove suspended solids (TSS) and colours, which reduces the amount of sludge produced and lowers the cost of sludge disposal. In the next step, a moving bed bioreactor (MBBR) further reduces organic contaminants and any remaining colour. With the MBBR technology, AWT was able to increase the capacity of the plant significantly, while keeping its footprint small. Finally, the effluent is filtered through sand and carbon, which ensures that the output effluent meets the requirements set by the Pollution Control Board (PCB). These systems are configured so that operating the entire plant is simple and semi-automatic. The plant was designed to handle 500 kilolitres per day (kld) with a peak capacity of 600 kld.
In contrast, the competing firm used chlorine oxidation in the pretreatment stage. This increases the total dissolved solids (TDS) in the effluent, and increases sludge production, as well as sludge disposal costs. In the secondary treatment phase, the solution was a conventional system that included extended aeration of the effluent. It requires a large footprint, which significantly increases the civil engineering costs borne by the client.
After several rounds of discussion with both parties, the client decided to go with AWT because our solution offered a smaller footprint, lower civil engineering costs and a guarantee that the outflow of the plant would meet PCB norms. Kathmandu Apparel awarded the contract to AWT in April 2018.
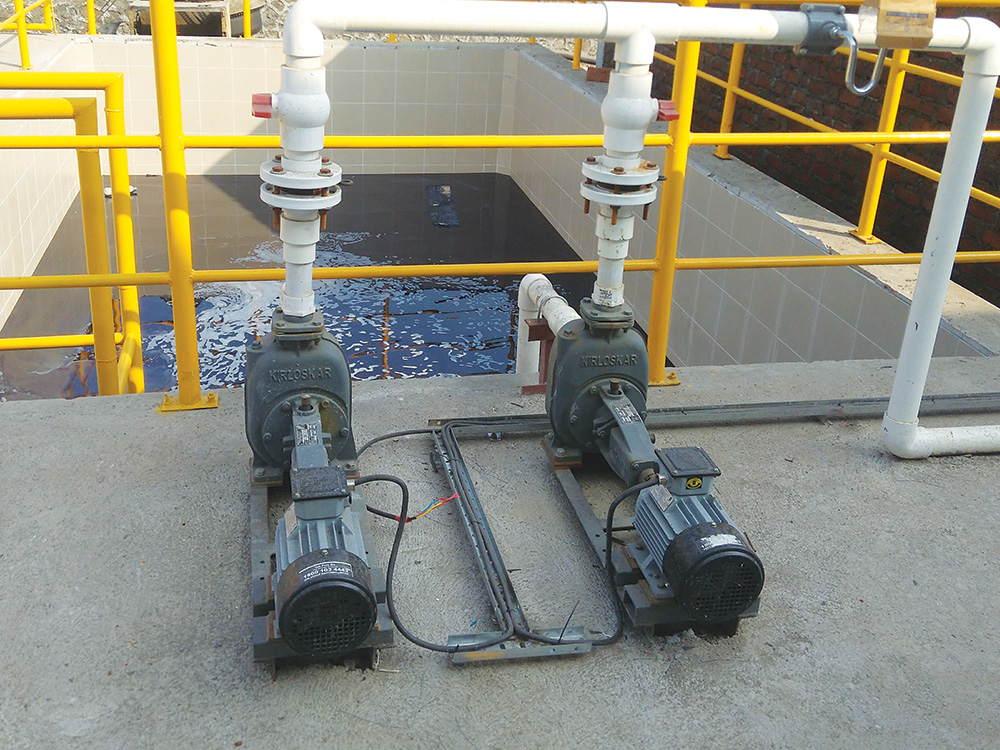
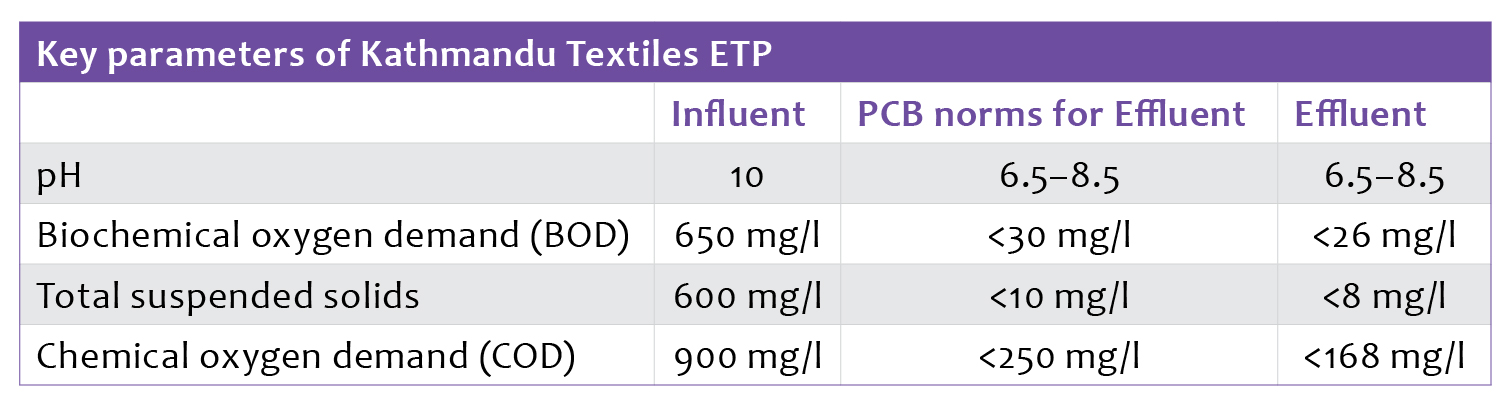
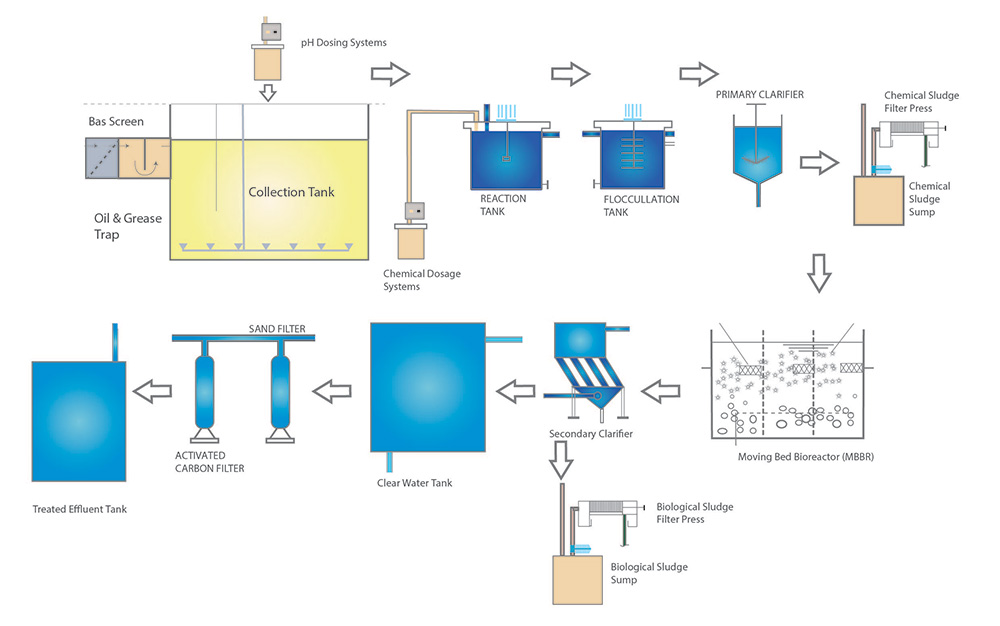